5 Green Star research winery signposts sustainability for New Zealand wine industry
Essentials
Name: BRI Research Winery
What: a cutting-edge research hub for the New Zealand wine industry focusing on viticulture and winemaking
Purpose: trials winemaking equipment, technologies, processes and sustainable winery operations. Provides commercial research winemaking services to suppliers and the wider industry
The building: a multi-functional facility comprising a functioning research winery, associated processing areas, a small office space and a conference room. The building has a highly specialised fit-out including a raft of custom-made fermentation tanks
Location: Within the Marlborough Research Centre on the Nelson Marlborough Institute of Technology campus
Where: 85 Budge Street, Blenheim
Occupancy: two to six people (dependent on season)
Project Snapshot
Owner: Bragato Research Institute (BRI)- Rangahau Karepe, Wāina O Aotearoa - is a wholly owned subsidiary of New Zealand Winegrowers – the national body for the grape and wine industry in Aotearoa
About BRI: spearheads world-leading innovation for the New Zealand viticulture industry. Established in 2017 with Ministry of Business, Innovation and Employment funding. While the research winery is Bragato Research Institute’s key asset it has other research programmes across the country
The Bragato name: Romeo Bragato was a visionary Italian wine expert who served as New Zealand government viticulturalist (1902-1909). He was instrumental in developing New Zealand’s wine industry
Architect: Jerram Tocker Barron Architects Ltd
Main contractor: Scott Construction
GSAP: eCubed Ltd
Project status: 12 month project; opened February 2020
Project certification: 5 Green Star Industrial Built v3 (November 2021)
At first glance the new BRI Research Winery in Blenheim might be mistaken for a standard winemaking set-up.
From the outside the contemporary-styled 752 square metre building - equipped with a mono-pitch roof, high clerestory windows above its winery hall and a large-scale canopy encompassing an outdoor work zone - gives little indication of its dynamic purpose or prominence.
But the research winery is far from ordinary.
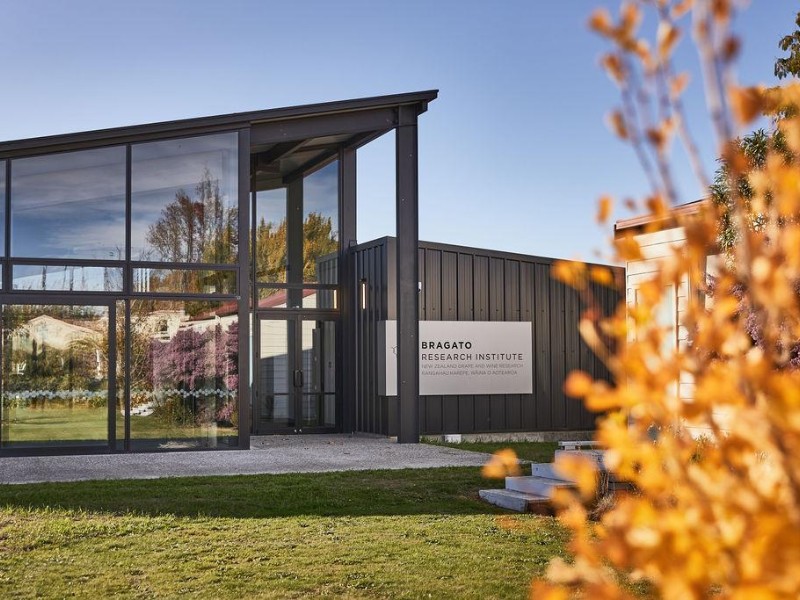
Not only is it a state-of-the-art facility for the advancement of wine science and viticultural practice in New Zealand but it’s the first Green Star certified winery building in the country, the first Green Star rated building in Marlborough and an exciting exemplar of green practice.
BRI Research Winery manager Dr Tanya Rutan says sustainability is fundamental to winegrowing in New Zealand and a new research hub was a chance to demonstrate that stance in a flagship building.
“Sustainability is central to so much of what we do. Currently 96 percent of the New Zealand vineyard producing land is SWNZ certified (an industry-wide sustainable winegrowing accreditation programme recognised as world-leading) with 90 percent of the wine subsequently produced in SWNZ certified facilities.”
She says the Green Star framework and New Zealand Winegrowers vision and goals are in alignment.
“Green Star certification was chosen for its global reputation and the high standards it delivers which show that Bragato Research Institute takes best practice for sustainability very seriously. A 5 Green Star goal was our target from the outset of the project.”
Tanya says the 'New Zealand excellence’ certification is “very exciting and we look forward to improving our sustainability practices even further and being a shining example for our wine industry.”
Project architect Simon Hall of Jerram Tocker Barron Architects says the research winery is designed to address the external and internal environment and sustainability.
“Each space has specific environmental and functional performance requirements and allowing interactivity and transparency between the differing spaces, which includes a glazed curtain wall between the conference room and winery hall, has been vital.”
“The use of insulation, daylighting and passive ventilation within the winery hall creates a fantastic stable and comfortable working environment for the scientists throughout the year with no active heating or cooling required,” he says.
Simon says the achievement of a 5 Green Star rating is “a great result especially as a first for Marlborough” and learnings from the project will be shared with others in the region.
He says Jerram Tocker Barron Architects has high levels of sustainability across all its projects.
“In future achieving 5 Green Stars and above is going to be critical to New Zealand’s ability to decarbonise its economy and importantly to delivering a better built environment for everyone’s benefit.”
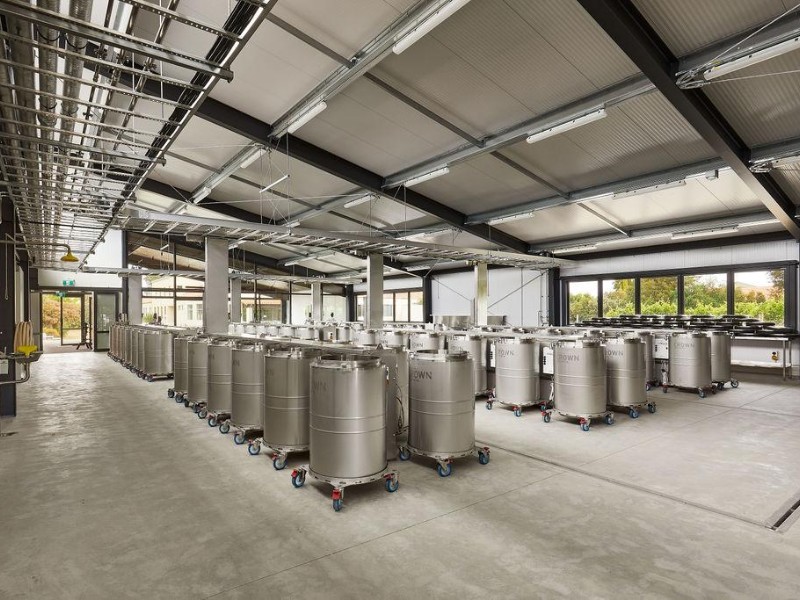
Patrick Arnold, Project GSAP and eCubed Ltd director says the BRI Research Winery is an excellent asset for an industry where the environment is incredibly important for continued growth.
“Internationally New Zealand has a reputation as green and clean and our wine industry trades off that name. We want to encourage and maintain that clean, green image with Green Star certified winery buildings. There has been plenty of interest from wineries in Green Star but it would be great to see increased certifications.”
He says Bragato Research Institute saw Green Star as a way of expressing and delivering its desire for sustainability and he hopes the message spreads.
“It’s so cool to see a pretty small research winery in Blenheim coming out with a 5 Green Star rating – it’s an absolute benchmark for the wine industry.”
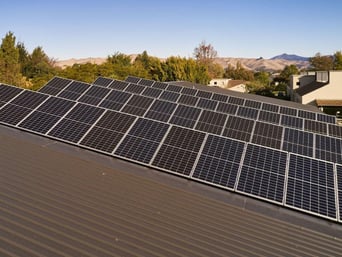
Patrick says the building’s green highlights include its PV solar panels (providing approximately 20 percent of the building's energy), rain water collection, water reuse and a range of sustainable building materials.
“BRI has worked hard to achieve 5 Green Stars with a few extra challenges along the way like restricted public transport in Blenheim and limited local recycling.
He says the research winery’s rainwater harvesting – which supplies all water fittings in the building not just selected fixtures – reflects how BRI has gone the extra mile.
“Despite being in the middle of Blenheim it will only use town water supply as a back-up during dry spells.”
Main contractor Scott Construction says building its first Green Star rated property has prompted the firm to think differently.
“We considered the volume of waste, recycling and diverting from landfill and responsibility around products such as low VOC paints and sustainably-sourced materials. It’s created a greater awareness in our team of the health and environmental benefits of a Green Star building,” says Scott Construction senior quantity surveyor, Chris Cooper.
“As a direct result of working on a Green Star project we’re more thoughtful and considered in our choices. We’ve had a change of culture and we have better waste management practices and FSC timber is now our first choice.”
Chris says Green Star is a badge the client can wear with pride and many people identify the brand
“Green Star is about being socially responsible and delivering a building that is better for the environment and the end user.”
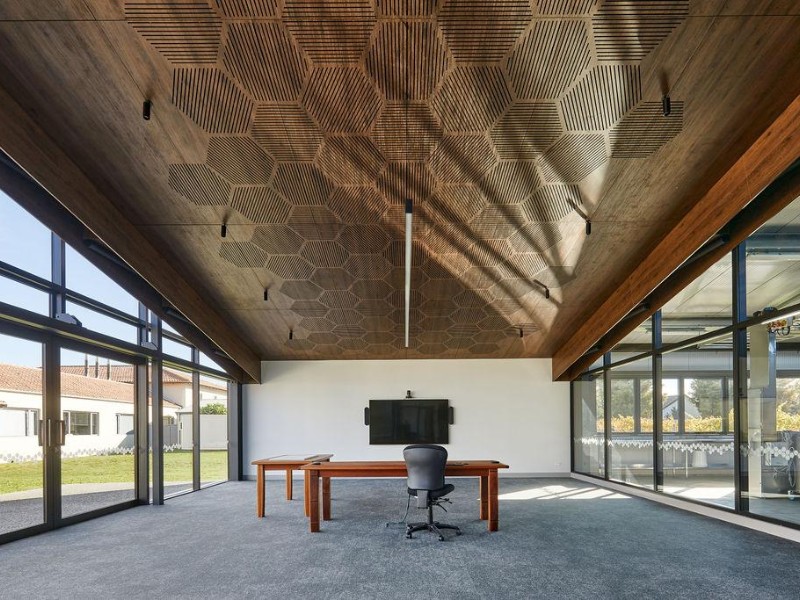
As the end user of the BRI Research Winery manager Dr Tanya Rutan couldn’t be happier.
“When I walk in each morning it feels uplifting with amazing natural light and a freshness and feeling that the design has somehow brought the outdoor environment inside and it fills our work spaces. Most days the natural light is so bright I don’t even turn on the lights.”
“There has been a lot packed into the building but it’s been thoughtfully laid out with an openness, easiness and accessibility – I’m never left thinking ‘if only that were somewhere else.’”
She says the research winery’s careful configuration and high-tech building management system has established an internal environment with “a sense of efficiency, high productivity and a general feeling of well-being.”
“As a scientist I feel so fortunate to be carrying out my role in a work space filled with natural light, brightness and great air quality – it’s the opposite of a windowless laboratory with artificial lighting. I appreciate it every day.”
Green features include:
|
Technical features include:
|