Countdown leads change with a dynamic green distribution centre
Essentials
Name: Palmerston North Regional Distribution Centre
What: 38,000 square metre (the size of four rugby fields) industrial facility comprising an internal distribution centre space, front offices and amenities, site and vehicular circulation
Purpose: Distribution hub for groceries delivered into 55 Countdown, Fresh Choice and SuperValue stores in the North Island
Where: 1-35 Alderson Drive, Milson, Palmerston North
Occupancy: 200 permanent full-time and part-time team members
Project Snapshot
Owner: PMB Landco Ltd and Carrus Turbo Holdings Ltd
Building Tenant: Woolworths New Zealand (Countdown forms part of Woolworths New Zealand, a subsidiary of the publicly-listed Australian company, Woolworths Group Limited)
Architect: Woodhams Meikle Zhan Architects
Main contractor: Watts & Hughes Construction
Project cost: $100 million
Project status: March 2020 to August 2021
Project certification: 4 Green Star Design Review Rating (July, 2021)
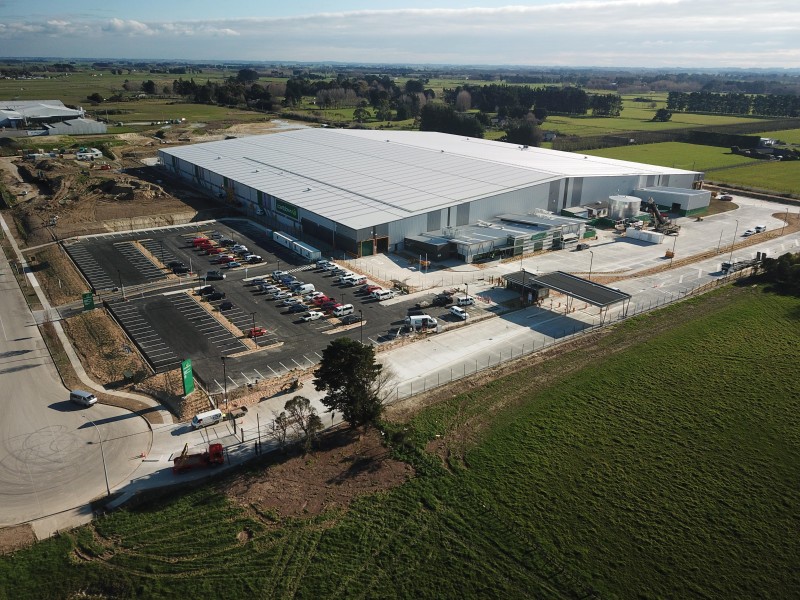
Warehouses, depots and distribution centres are not typically buildings linked with cutting-edge green design.
But Countdown’s new Palmerston North Regional Distribution Centre on the outskirts of the city showcases a forward-thinking approach.
With the environment, energy efficiency and occupancy experience at its heart, the state-of-the-art facility has been awarded a 4 Green Star Design Review rating reflecting ‘best practice’
“The whole building itself is exciting. But we’re particularly excited there are features that not only make the building more sustainable - energy efficient lighting, low water use plumbing fittings, rainwater harvesting, all electric manual handling equipment etc - but also help our team to lead more sustainable lives too with EV charging facilities and bike parks, and the increased natural light and space makes it a really great environment to work in,” says National Non-Retail Property & Development Manager, Bruce Waite.
Those inspiring green features Countdown has applied to the new Palmerston North distribution hub are resonating well beyond its walls.
In a benchmark move the supermarket chain has committed to achieving a 4 Green Star Design and As Built rating for all new developments – with a 5 Green Star minimum rating by 2025.
The pledge sits at the heart of Countdown’s 2025 Sustainability Plan, Kia pai ake te āpōpō - a better tomorrow.
And it is a commitment that has created a new green point of reference.
“We’re really proud to be setting the benchmark for other large retailers in Aotearoa,” Bruce says.
While the Palmerston site is Countdown’s first Green Star rated distribution centre, its first Green Star rated supermarket has opened in Richmond, a second opens shortly in Auckland and an additional Green Star distribution centre is underway.
Bruce Waite says Countdown’s stores and distribution hubs have a huge role to play in helping us to reduce our impact on the planet.
“Green Star is well-recognised, trusted and delivers the support and knowledge we need to help us build better. Working with Green Star has also meant we’re now well-connected with the people, products and services we need to deliver sustainable projects.”
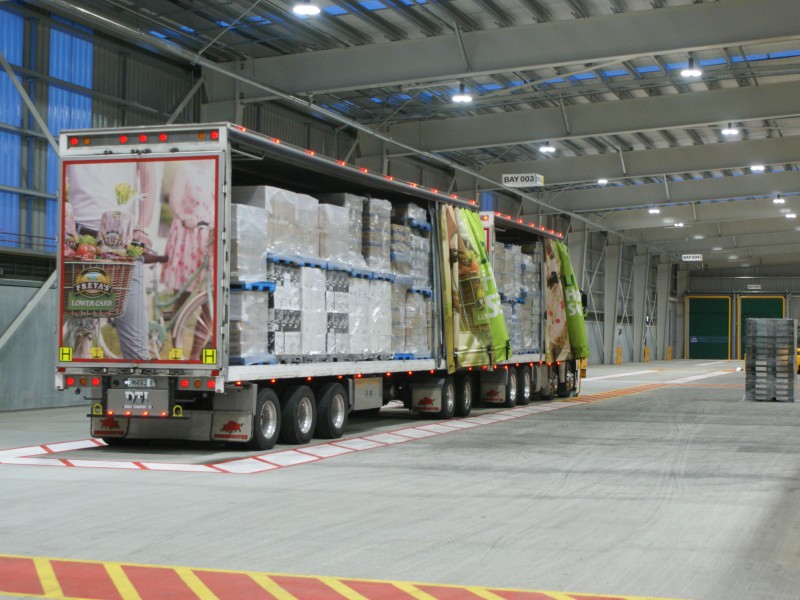
General Manager of Corporate Affairs, Safety and Sustainability Kiri Hannifin says Countdown is determined to make sure it’s not just creating buildings 'of the future' but buildings that help protect that future too.
“Green Star is fantastic because it encourages our team to try new things, to build new ways and to think outside the box when taking on our development projects.”
Countdown says the Palmerston North Regional Distribution Centre’s 4 Green Star ‘best practice’ rating is a source of pride and has added value to its brand.
“We’re really pleased with the rating. It’s a reflection of Countdown’s commitment to build and operate in a way that doesn’t impact the environment and the hard work of the consultant and construction teams,” Bruce Waite says.
Among those consultants is project architect Bradley Wynn, director at Woodhams Meikle Zhan Architects, who believes certification should be considered “beyond important in today’s world.”
While the design was underpinned by the need for a highly functional and safe space for people and vehicles, it also allowed for the inclusion of sustainable elements.
“We’ve used this functional requirement to introduce a variety of spaces and volumes to give people the benefit of space, openness and natural light as they move through the buildings.”
Key elements include good building orientation, natural lighting of key occupied spaces, a high level of acoustic performance in staff areas, above code levels of insulation, integration of natural light and ventilation into the large distribution space, and careful selection of sustainable materials.
“These features contribute to a workspace that is healthier and more comfortable to work in. This can only help to allow people to carry out their work at a better level both physically and mentally,” says Bradley.
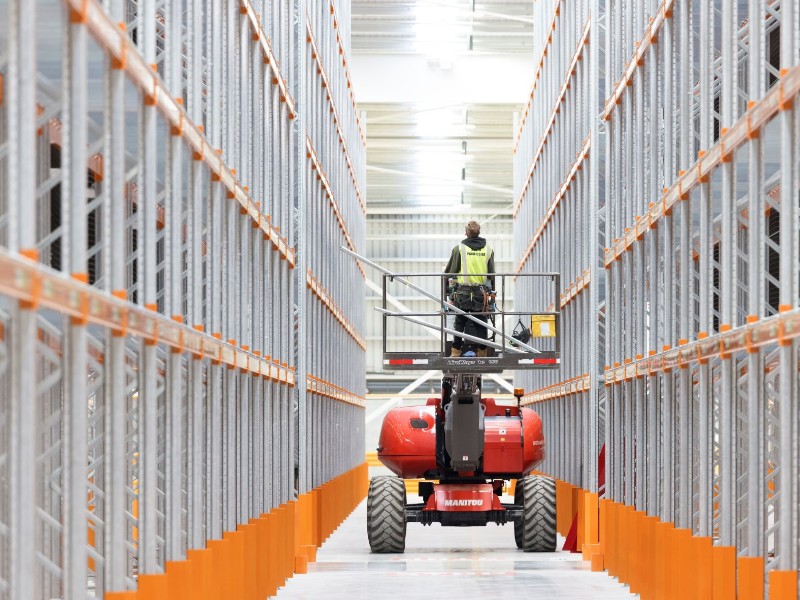
Project GSAP and eCubed Building Workshop Ltd associate Ella Osborne says food supply and distribution is an undeniably important issue.
“It is great to work with an organisation looking to reduce the environmental impacts associated with the food journey.”
“It’s been fantastic to be part of the team delivering Countdown’s first large-scale Green Star rated industrial building and it’s also exciting to be part of a green project outside our main cities as it brings challenges and opportunities.”
One of the challenges posed by the Palmerston North project was how to recycle over 5 tonnes of GIB offcuts generated during the build with no GIB waste processing in Manawatū.
“The solution was such a cool initiative. GIB recycling facilities in New Zealand are currently limited to only Auckland and Christchurch (Green Gorilla depots) but main contractor Watts & Hughes identified the backload capacity of Countdown trucks could transport GIB offcuts back to Auckland for recycling with no additional transport emissions incurred in the process,” says Ella.
As a result Countdown is now looking at other connections in its transport network to help improve waste recovery and recycling for future projects in regions with limited local waste processors.
Palmerston North Regional Distribution Centre project manager Monique Sullivan of MPM Projects, says it’s great to see green knowledge and green solutions bring shared outside the main city centres.
Using that green knowledge has been centre stage for Watts & Hughes Construction. During the Palmerston North project it developed a best practice site-specific environmental management plan which it is now using as a template for other builds on its books.
Watts & Hughes Contracts Manager Jonathan Tindall says Green Star raised environmental awareness with all stakeholders during the build. Waste management requirements in particular were a hot topic at on-site Green Star meetings.
“In the past recycling and reducing waste to landfill was just an optional extra but Green Star really changes your attitude and helps give us that extra push. With Green Star support on a project you can really see what’s possible and how a development can minimise environmental impacts and improve sustainability during the build and into the lifespan of the building.”
Jonathan says the construction sector’s high contribution to landfill is a real concern and the whole industry is capable of making huge improvements.
That pathway, performance and lifespan of the Palmerston North Regional Distribution Centre is already shaping up well.
Energy modelling demonstrates it is currently achieving a 60 percent reduction in operational energy and CO2 emissions compared to a standard building.
And feedback from the Countdown team has given the new site a big thumbs up.
"It's light, bright and the whole environment feels clean and fresh with great airflow and CO2 monitors delivering the best internal atmosphere,” Countdown Supply Chain Manager Scott Bennett says.
“From the staff cafeteria, to the offices, to the distribution centre there’s just a great feeling of spaciousness and beautiful natural light everywhere. I think our team is uplifted by the whole new setting.”
“Our staff cafeteria has great indoor outdoor flow and food wastage here is absolutely minimial. Even though the building is industrial looking everything has been done to soften it in the landscape with little touches everywhere like attractive planting around the carpark.”
National Non-Retail Property & Development Manager, Bruce Waite says Green Star certification is the way forward.
“We’re already seeing the impact the climate is having on our weather, our wildlife and our oceans. Green Star and the framework it has created to help businesses like ours to design, build and operate more sustainably must continue to be a really important part of Aotearoa’s climate response.”
Green features include:
|
Technical features include:
Innovation points awarded:
|