Foodstuffs North Island (FSNI) Head Office is located at The Landings, Mangere, Auckland. The proposed development consists of a new three-storey office building. The building is designed with a central atrium to increase daylight penetration which separates the east and west areas of the floor plate. The ground floor consists of office spaces and conference centre facilities to the west half of the floor and public cafeteria / restaurant and associated kitchen areas to the east half of the floor. The first and second floor are predominantly large open plan offices.
The building is to be constructed from concrete slab floors, with profiled steel roofing, concrete panel walls to the east and west facade and curtainwall glazing to the north and south facade. The window-to-wall ratio (WWR) of the building, excluding the plant rooms, is 54%. The building itself takes the form of an earth mound with large roof overhangs and bunding to the east and west sides.
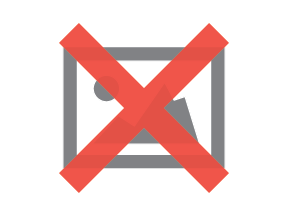
There are plant areas on the ground floor to the east and west sides of the building. There is also a large distribution centre / warehouse on the same site to the south of the office. The warehouse has been modelled, though due to the orientation does not result in any overshadowing to the office. Aside from this there are no other buildings in the surrounding area. The warehouse and site orientation are shown in the image below
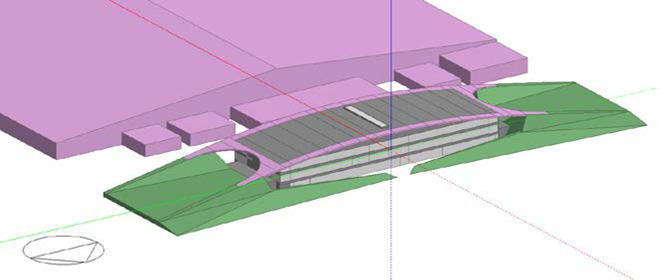
Project Details
Rating awarded: 5 Green Star Office Design v3
Project location: Te Kapua Drive, Mangere, Auckland
Building owner: Auckland International Airport Limited
Architect: Monk Mackenzie
Project manager: TSA Management
Service engineer: eCubed Building Workshop / Electrical Consulting Services
Quantity surveyor: Rider Levett Bucknall
Main contractor: Hawkins
GSAP: Ella Osborne, eCubed Building Workshop
Acoustic consultant: Norman, Disney and Young
Fire Engineers: Holmes Consulting
Key sustainability features
Management
- Construction waste management was implemented. Target > 70% demolition and construction waste to be reused/recycled. A construction management plan was developed by the contractor including project specific response to resource consent conditions, environmental protection and health and safety.
- The contractor Hawkins is ISO 14001 certified and provided a site-specific environmental management plan for the project to minimise impacts during construction.
- Best practice testing and commissioning of the building services in accordance with CIBSE standards was carried out under the supervision of an independent commissioning agent
- A first year building tuning process of the building services will be undertaken under the supervision of the independent commissioning agent.
- An extra 4% of the construction budget was expended on environmental features including the targeted 5 Green Star environmental rating.
Internal Environmental Quality
- HVAC systems will have CO2 monitoring and control facilities.
- Where appropriate and with due regard to durability low toxicity materials will be used including adhesives, paints, sealants, carpets, ceiling tiles and composite timber board products.
- Local exhaust systems will be provided for kitchenettes, utility areas toilets and end of trip facilities.
- Daylighting, transparency and views/outside awareness are key design features.
- Lighting levels meet AS/NZS 1680 standards and the design lighting quality and surface finishes reveal/enhance the office spaces and ambience.
- A high-quality acoustic environment is provided.
Energy
- A large scale photovoltaic (PV) array on the distribution centre roof which generates renewable energy from the sun for both the office and distribution centre.
- An energy efficient façade is provided with double glazed low e IGUs with selective coatings for control of heat loss and heat gain. Highly insulated roof and moderately insulated walls to suit the high internal gains within the building.
- Cooling of the building uses high efficiency air cooled chillers (seasonal COP 5.04).
- High efficiency variable speed pumps and fans with CO2 control of outdoor ventilation rates to suit occupancy and variable volume chilled water distribution to suit demand.Use of energy efficient EC fan coil units with variable speed occupancy control and setback.
- Non fossil fuel current valve controlled electric heating within fan coil units (approx100% efficient).
- Good levels of natural light during daytime hours.
- Low energy lighting will include 100% use of LED lighting and an automated lighting control system.
- Efficient external LED feature lighting and controls.
- A building management system is provided with main and sub electrical metering for energy management including integration of adjacent distribution centre systems.
Transport
- Foodstuffs will develop a site-specific staff travel plan.
- Staff will be encouraged to use public transport or cycle where possible and noting the current lack of infrastructure in the regard at present and future Auckland Transport initiatives.
- A total of 85 car parking spaces in the car park are reserved for fuel efficient or carpool vehicles. There are also 43 motorcycle spaces.
- There are 6 dedicated EV parking spaces with charging facilities.
- Staff bicycle storage and end-of-trip facilities will be provided for up to 60 users. Bike parking will also be provided for building visitors.
Water
- Low water use plumbing fittings are used including sensor taps and timer showers.
- Water metering is provided for the potable water system linked to BMS.
- Rainwater harvesting is included for non-potable toilet flushing and building washing purposes.
Materials
- Environmentally certified and labelled materials including paints, insulation and plasterboard, carpets, ceiling tiles, FSC timber framing and select composite boards. Select products with third party accredited EPDs.
- Very low formaldehyde wood board products or phenol formaldehyde bonded plywood are used.
- Low VOC, water-based glues and paint finishes are used.
- Timber and timber products sourced form FSC certified forests with full Chain of Custody
- All concrete and concrete products used in the building meet minimum environmental criteria as follows;
- The mix water contains at least 50% reclaimed water (averaged across all concrete used)
- 25% of cement in in situ and 15% of cement in precast concrete is replaced with Fly Ash or other inert filler.
- Cement is sourced from manufacturers that use 10% alternative fuel, such as Golden Bay cement.
- The building includes a designated space for the collection, separation and storage of waste.
- Best environmental practice certified PVC used for all plumbing pipes and electrical cables.
Land Use and Ecology
- The 100-hectare Landing development is a strategically located multi-stage comprehensively planned warehousing and logistics precinct located between public open space to the north and a proposed extension of the Auckland Airport Activities Zone to the south.
- The Landing’s design features and materials draw on the surrounding environment and previous land use to create a manicured and high amenity setting. The Landings infrastructure includes “feature landscape” stormwater detention ponds within existing wetland areas that include an in situ concrete weir, inlet and outlet elements, and loose basalt rip-rap to pond banks and bunds.
- The site is adjacent to the Oruarangi Creek to the North and 10 hectares of parkland are being created beside the Creek. The parkland will feature walking and cycling tracks for the enjoyment of both tenants and the public.
- The nearby historic Otuatua Stonefields is referenced by stone mounds rising within roundabouts. These mounds are lit at night with colours inspired by the New Zealand landscape, from Huka Falls to the volcanoes in Auckland.
- A mix of native and non-native species has been used to reinforce the vision of the Airport landscape as a blend of native and cultural landscapes, and to create a clear and legible roading hierarchy. Planting consists predominantly of native garden planting, incorporating various native understory shrub species and native trees. Typologies include: - Large areas of mass-planted drought-tolerant sedge and rush species.
- Native amenity gardens with mixed native species such as flax, ferns, lilies, and sedges.
- Native tree planting including Pohutukawa, Titoki, and Nikau.
- The surrounding roads break from the native palette and feature exotic tree planting in the streetscape design including London Planes and Lombardy Poplars. The Landing has an axial roading framework. Primary roads are aligned east-west, with secondary roads aligned north-south. Each road type is comprehensively designed to encompass the roading corridor, front yards and front yard boundaries between adjacent sites. The street landscaping principle of street trees, hedgerows and native grasses incorporates car parks in front of sites to reduce vehicle prominence.
- Site earthworks included preloading the area under the building platforms and moving soil to areas where public open space landscaping will occur in the future.
- Areas surrounding the site are allocated to be used as public open spaces to make the area social, friendly and relaxing.
Emissions
- Zero ODP refrigerants and insulants were used.
- Sanitary water quantities were used reduced using low water use sanitary fixtures.
- Filtering of contaminated surface stormwater has been included via low impact gross pollutant traps and swales.
- The building is compliant with Resource Consent conditions regarding light and noise pollution