A window to the future – 5 Green Star rating showcases sustainable industrial design
Essentials
Name: Profile Group Hautapu Facility
What: The first building to be constructed in a 56.7 hectare green-visioned industrial campus bordering the Waikato Expressway near Cambridge. The masterplan creates a self-serviced industrial park with sports, childcare and health facilities
The building: Just under 49,000m2 (the size of six rugby fields) it comprises a factory and three linked double-storey office buildings with viewing platforms/windows into the manufacturing hubs, meeting rooms and staff break-out areas accessing landscaped spaces and pathways
Who occupies the building: Architectural Glass Products (AGP), a state of the art double-glazing manufacturer, and APL Manufacturing (APLM), a division of APL Window Solutions – the country’s largest manufacturer of aluminium windows and doors, est 1971. APLM manufactures entrance doors, hardware and rooflights to their fabricator network. Both AGP and APLM are key players in Profile Group (PGL) – the unifying platform for New Zealand’s only integrated supply chain for window and door solutions and the entity behind the Hautapu industrial campus.
Where: 137 Swayne Road, Cambridge, Waikato
Occupancy: 200 people
Project Snapshot
Owner: Appropriate Holdings Ltd
Architect: Jasmax
Structural Engineer: BCD Group Ltd
Service engineer: eCubed Building Workshop
Main contractor: Foster Construction Ltd
GSAP: Ella Osborne, eCubed Building Workshop
Project status: commenced early 2019; fully completed December 2021. Approx. 400 workers on site during peak build period
Project certification: 5 Green Star NZ v3 Industrial Design rating (December 2020)
A manufacturing plant in a new industrial park might sound a world away from any visionary green thinking.
But Profile Group Hautapu Facility on the outskirts of Cambridge has the care and custody of the environment and its employees at its core.
The newly-constructed low carbon manufacturing hub has set a benchmark for industrial design in Aotearoa and achieved a 5 Green Star industrial design rating.
Parent company PGL says the New Zealand excellence design accolade reflects its advocacy for the principles of green building.
“We pursued a Green Star rating because as developers and building owner/occupants we place a huge amount of importance on building high quality buildings. We don’t believe in cutting corners, we’re passionate about impressive architecture and design, and we take our responsibility to protect the environment seriously when achieving that,” says Mikayla Plaw, PGL executive director.
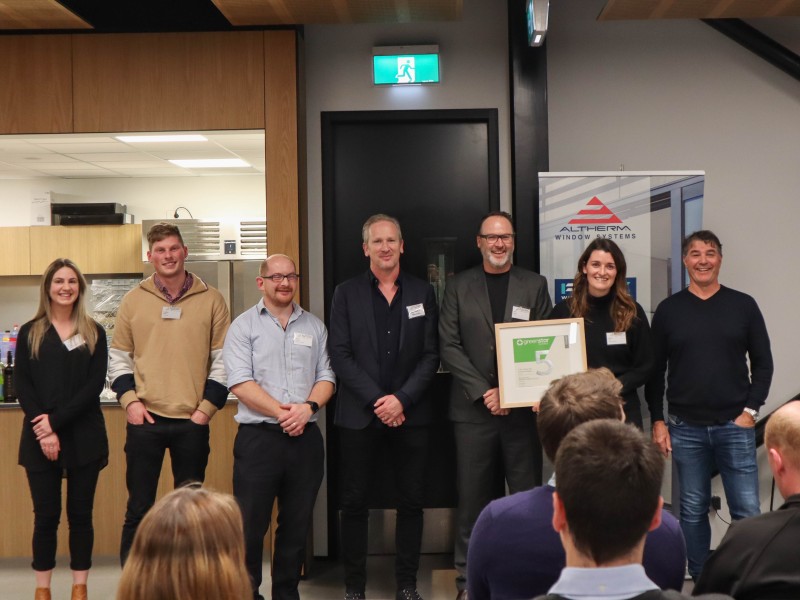
“As a group of businesses Green Star aligns with our values. We’re always looking forward for the next opportunity while constantly working on improving today – we do this for our people, our communities, our industry and the environments in which we live and work.”
She says PGL hopes it can inspire others who are developing large-scale buildings to design and build to a Green Star standard.
Jasmax Principal Nick Moyes, who led the design team, says the accreditation marks the practice and wider project team’s commitment to sustainable, future-focused design.
“Any project with sustainability at its core starts with collaboration. Our vision for the manufacturing plant was developed jointly, with an integrated design approach, and most key green goals and initiatives were conceived together.”
He says a key aspect of the project’s sustainability was joining the dots between the scale of the building and the need to achieve “peak-efficiency.”
“Foster Construction played an integral part in bringing the most efficient and effective construction methods to the project, centred on a philosophy of design excellence established by PGL,” Nick says.
He says one of the most exciting features of the project came from ensuring the day-to-day experience of staff working in the facility was central in design decisions.
“For example daylight and exterior views were a massive design consideration, and led to the inclusion of five huge skylights. These minimise the need for artificial lighting and allow most occupants to connect to the outdoors - something that’s so often missing from manufacturing facilities.”
He says the fantastic 5 Green Star result validates the project’s holistic approach to sustainability, combined with a drive for efficiency.
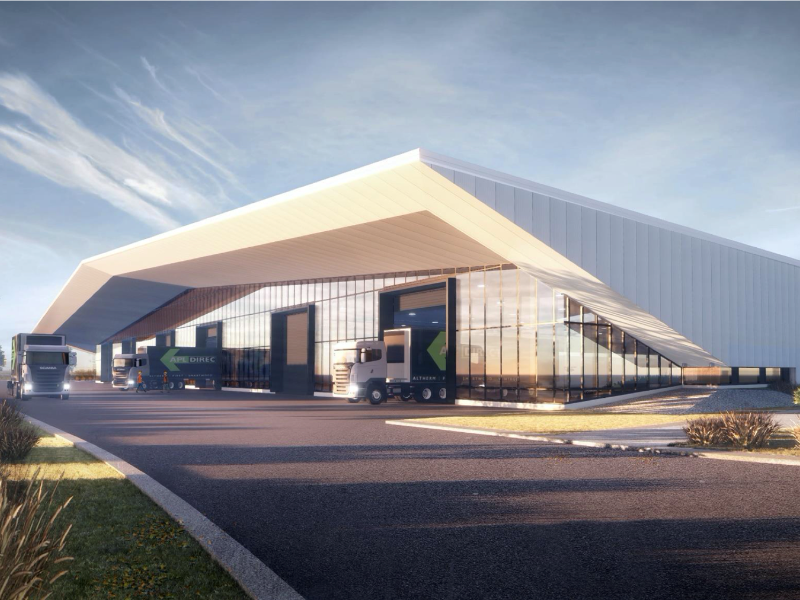
Project GSAP and eCubed Building Workshop Ltd associate Ella Osborne, says the project has had a strong focus on the natural environment, stormwater planning and energy conservation.
Highlights include:
- Enhanced ecology and water sensitive design principals to replicate natural water systems and recharge the wetlands basin at the campus.
- Three million litres of water run-off stored in an on-site pond annually providing water for fire-fighting storage, toilets and irrigation.
- The use of a post tensioned concrete slab which reduced overall concrete and reinforcing steel compared to a traditional slab - combined with a water curing surface treatment eliminating the need for applied sealers.
- Optimised factory skylight design for natural lighting combined with highly efficient lighting systems including dimming controls and daylight sensors - resulting in a reduction of over 500,000 kWh of lighting energy annually.
- The building is currently achieving a 40% reduction in energy and CO2 emissions due to efficient design.
Ella Osborne says large-scale construction can be so damaging for the environment but the AGP Manufacturing Facility demonstrates best practice.
“I’m so impressed with the commitment from everyone in the team to put sustainability at the core of the design and delivery of the building and I’m also just impressed with what the Hautapu project is all about – producing high performance glass products and window systems locally in New Zealand – something which in turn links to the design of many other green buildings.”
Main contractor Foster Construction Ltd (which holds Toitū Enviromark Diamond Certification verifying its environmental management systems exceed the internationally recognised ISO 14001 standard, and is registered Toitu Carbon Zero measuring operating carbon footprint) says constructing a Green Star project has impacted on its day-to-day activities - from selecting sustainable materials through procurement, managing and monitoring products brought to site and recycling construction and demolition waste.
“We’ve had to rethink the way we construct certain elements to meet the Green Star criteria,” says Foster Construction Ltd, sustainability and compliance advisor Jael Clausen.
“Working on a facility of this scale and knowing it has been built sustainably has been a personal highlight for me. I’ve also had the privilege of witnessing the positive change this project has had on our overall construction practices to build sustainably,” she says.
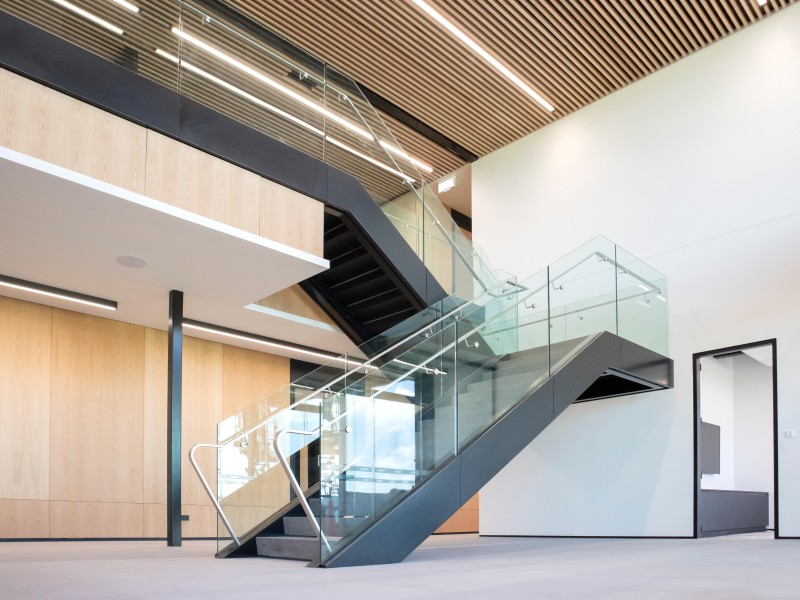
PGL executive director, Mikayla Plaw says the 5 Green Star result has been underpinned by an enormous collaborative effort from everyone in the design team through to the engineering, construction team, subcontractors and the building occupiers.
And she says the building’s green credentials are having an overwhelmingly positive impact on staff.
“People are loving the building - there’s lots of natural light, lots of places to relax during break times and the comfort factor inside the factory is great. One feature our occupants are really excited about is our bike centre. Employees can bring their bikes in off the road, store them safely, leave their belongings in the lockers provided, have access to the beautiful shower facilities and head out on to the floor.”
Other members of the PGL workforce say the design of the building enhances their working day.
“I love the design of the interior as well as the exterior – the wood finishes and furnishings make it feel close to nature, the large windows flood the office with natural light and the warm lighting transforms our workplace into an inviting zone which fosters creativity and more motivation. I love working in our new site – it’s very calm and inviting,” says APLM accounts administrator, Jennifer Deniega.
APLM finance and accounts supervisor, April Chen, says the attractive work environment is peaceful and enjoyable for staff and will increase workforce productivity, staff engagement and make people look forward to coming to work.
“The central air con creates the most comfortable temperature for the workplace while sensor control hand dryers, lights, sensor taps and energy saving lights programmed to be turned off after certain time all reduce the consumption of energy usage. PGL is continually looking after its employee workplace and wellbeing – even weekly fresh fruits and nuts sourced from local supplies are delivered to our office.”
Green features include:
|
Technical features:
|