Transforming an earthquake-damaged Christchurch homestead into a sustainable, low energy family home has been a journey of challenge, love and commitment for its owners.
And amplifying that challenge has been a highly detailed and dynamic rebuild project framed by stringent performance specifications.
Now the family’s aspirations and efforts have been rewarded with an exceptional double certification.
Refurbished Woodford Grace Homestead and its new pavilion-style extension has achieved a Passive House Institute Low Energy Building certification and an 8 Homestar certification - providing a great example of how the two benchmarks can work together.
Essentials
Owner: Dorset Family Trust
What: 1920s two-storey weatherboard homestead damaged in the 2010/2011 earthquake; sold ‘as is where is’; four bedroom homestead extensively retrofitted while retaining its character; a new single-level pavilion-style extension comprises kitchen, utilities areas and a downstairs bedroom; the completed new-look residence is 350m2
Name: Woodford Grace - the homestead was named Woodford after an area in east London where the property’s original owner spent their childhood. Grace is the name given to the pavilion, acknowledging the owners’ daughter Grace who was stillborn
Where : Carlton Mill Road, Ōtautahi Christchurch
Occupancy: two adults and three children
Project certification: PHI Low Energy Building certified by the Passive House Institute (2021). 8 Homestar rating (2022).
Project award: silver award 2021 ACE New Zealand (Association of Consulting and Engineering)
Project Snapshot
Architect: Cymon Allfrey Architect
Landscape architect: Rough Milne Mitchell (RMM)
Main contractor: Philip Jacobs Building Services
Homestar assessor: Michelle Abley
Project timeline: purchased 2016; occupied June 2020
When the Abley family purchased an empty house - out of alignment with quake-damaged foundations and broken plumbing and electrical infrastructure - they identified three key drivers for modernising the dilapidated dwelling.
“Warmth, comfort and wow factor were at the heart of our detailed written brief,” says homeowner and property manager for the redevelopment, Michelle Abley.
Attracted by the homestead’s close proximity to central Christchurch and Hagley Park , as well as its generous 2200m2 section, the family staged a small-scale architectural competition to secure designs for a modernised homestead and integrated grounds.
“We paired up three teams with an architect and a landscape architect in each as we wanted the landscape design to work in tandem with the homestead rather than being an add on at the end.”
Michelle says while sustainability, comfort and low energy outcomes were always central to the project, PHI Low Energy Building and Homestar certifications were not goals at the outset.
“We were already on the pathway to build a high performance home without knowing these frameworks and tools existed. PHI and Homestar happened along the way as a means of delivering and benchmarking the passive and sustainable elements of the house. Utilising these two benchmarks to test and assess along the way provided us with better quality measured outcomes.”
Michelle says there is a clear alignment between the two, and by targeting a Passive House certification the project was already setting itself up for a Homestar rating.
“A large component of Homestar is building performance and Passive House modelling is a very effective way to achieve correct outcomes. This feeds directly into compulsory Homestar credits.”
Midway through the four year project Michelle qualified as a Homestar assessor.
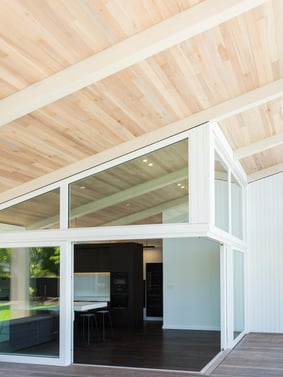
“I have a strong interest in sustainable thinking around the built-environment and as project manager for Woodford Grace it made sense. Initially qualifying as Homestar assessor was to learn and put into practice initiatives for our project. It has since turned into a longer term career pathway.”
More recently she has qualified as a certified Passive House consultant.
Michelle’s skill base has been an asset given the project’s “geometrically complex shape” and the challenge of joining the old house (largely rectangular) with a more complicated pavilion with a raking ceiling and multiple angles.
High quality internal timber wall linings - generally Rimu- in the entrance and stairwell of the original homestead have been retained (remaining in situ during the deconstruction/ construction process) and all internal doors have been revitalised and reused.
A large amount of surplus timber was sold to second-hand dealers to reuse in other projects.
With the decision made to pursue a PHI certification after the house design concept was finalised, Michelle says the old homestead was always going to be challenge.
Those challenges included:
- the difficulty of achieving air tightness (particularly around the midfloor and stairwell which have been retained)
- getting enough insulation installed (removing the dwangs in 90mm stud walls to increase insulation/added a 45mm internal cavity)
- reducing thermal bridges
- achieving new triple glazed timber windows that looked ‘old’
- incorporating the original stained- glass windows to achieve the required thermal standard (the stained glass is now set inside a triple glassed/glazed window framed in Siberian Larch)
- the challenge of fitting the Mechanical Ventilation with Heat Recovery (MVHR) ducting
Similarly delivering sustainability in the pavilion required some problem-solving.
“It has a large amount of glazing including a large opening corner slider with windows above. This was difficult to achieve as some steel needed to be used structurally. At the same time the join between the pavilion and the existing house required a large steel portal. Insulating this properly within the space allocated was challenging,” says Michelle.
While navigating air tightness and low energy performance specifications might have prompted some owners to revisit their goals, Michelle says they stuck to the key outcomes of their original brief despite time and cost increases.
“We were determined to achieve a PHI certification and persevered even when it felt impossible to achieve.”
She says seeking a Homestar rating in addition to a Passive House Institute certification was a natural progression.
“The PHI certification demonstrates our house performs well for warmth and comfort and it centres on the detail and analysis of the building fabric. Homestar demonstrates we have included other sustainability features such as sustainable materials, water flow rates and landscaping elements. There is a strong connection between the two.”
As Homestar assessor, Michelle says the key sustainable features of Woodford Grace homestead include:
- a super insulated building envelope
- highly efficient ventilation system
- triple glazed fully sealed German manufactured timber windows
- airtightness layer - a combination of membrane system and plywood joinery
- 16kW air to water heat pump linked to a 300 litre hot water cylinder/central heating system
- Zehnder MVHR system (mechanically sucks external air in and distributes it around the house via a series of ducts)
- ground sourced loop attached to MVHR for pre-warming/pre cooling
- solar PV array
- water efficient taps, shower heads and toilets
- low energy consumption (28kWh/m2)
Oculus principal analyst and Passive House designer for the project, Denise Martin, says the energy efficiency of Woodford Grace is a stand-out green feature.
“Energy efficiency is the first renewable energy because it doesn’t need to be generated and hence doesn’t require any upfront carbon emissions. The efficiency comes from scientific evaluation and not from green or sustainable features. It’s created by optimising the building fabric instead of (only) using energy efficient appliances to heat and cool the building.”
Main contractor Philip Jacobs of Philip Jacobs Building Services says the 8 Homestar rating and PHI Low Energy Building endorsement for Woodford Grace recognises the hard work behind the scenes.
“With electrical holes and plumping holes in the original house going right down through the bottom wall plates into the sub floor area for example, this project has been a challenge,” he says.
“But with good communication from the Passive House designer, engineer, good subbies and a strong relationship with the owners we got there and it all helped to achieve the highly detailed requirements for the build. It is a project that I will always be proud of.”
Michelle says that teamwork and communication has underpinned the success of the project.
“It has been absolutely a collaborative effort. The team had to work together to find solutions to the many challenges we encountered.”
So after two years of living at Woodford Grace homestead has the challenge of redeveloping the large-scale property been worth it?
“The effort that has gone into upgrading an old and cold Christchurch house into a warm, comfortable and healthy home cannot be understated,” says Michelle.
“The house is incredible to live in and it enhances our lives. The warm environment, the way in which the house is so original with both the old and the new, the space for our family, the rooms within the house are lovely, the landscape and garden is beautiful. We feel very privileged to live here.”
She says often during the Christchurch winter the family has no idea what temperature it is outside, as the house is consistently warm.
“Our internal climate sits between around 20 to 22 degrees and the house is warm in winter and cool in summer.”
The family’s heating bill stays low with central heating only run during the middle of winter for a couple of hours per day.
She says measuring the performance of a house is crucial and Homestar has the language and toolkit to propel the industry towards greener and more sustainable homes.
The current Building Code, she says, “is a long way from delivering warm and comfortable homes for New Zealanders.”
“By assessing and certifying your project with Homestar you are showing you have achieved actual quantifiable results. You have to be rigorous through the project and not cut corners.”
“Don’t shortcut the process if you can afford to keep going. Certifying your building also makes you measure and assess so you achieve the desired outcome rather than being ‘close enough’.”
She recommends those embarking on a project targeting a Passive House or Homestar certification design for the certifications right from the outset.
“If you can afford to spend the money on upgrading your building to Passive House or Homestar standard you should do it. Get advice from Passive House and Homestar experts early in the process. The environment you create is so worth it.”